.jpg)
As we maneuver into the next phase of recovery and live alongside the pandemic, various challenges will arise as we deal with new strains such as Omicron, and the large case numbers that come with living with the virus.
The biggest challenge troubling the technology industry is unprecedented lead times resulting from global supply chain issues.
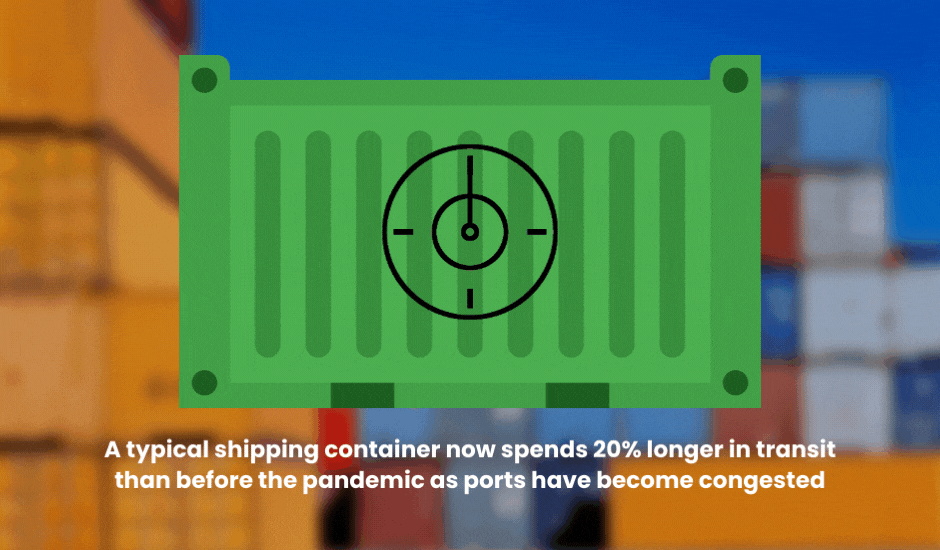
According to Fast Company, a typical shipping container now spends 20% longer in transit than before the pandemic as ports have become congested.
A combination of disruptions stemming from the pandemic including labour shortages, increased consumer demand for goods and products, cyberattacks, ‘The Great Resignation’, as well as other global factors has hit tech companies hard, causing unprecedented delays and backlogs. Despite efforts from both the public and private sector, experts predict that supply chain-related issues will persist into 2023.
The current Omicron variant has particularly been problematic due to the strain being more contagious than previous strains, which has seen more people take sick leave or isolate due to being a close contact, as well as suppliers needing to navigate new restrictions. On top of this, China – the world’s largest manufacturer – throughout the pandemic has committed to a zero-COVID strategy, which is likely to continue. This strategy severely disrupts both the production and transportation of goods, and it doesn’t look like China’s stance will change anytime soon.
Businesses across the globe are attempting to prepare for the “new normal” by gearing up all the resources and capability needs required such as installing video conferencing rooms to support a hybrid workforce, and virtual meetings, as we deal with Omicron and future strains. However, due to these supply-chain issues, it’s becoming harder for businesses to meet their expected deadlines.
Willy C. Shih from Harvard Business Review suggests that a tech companies should hold intermediate or safety stock and determine how much extra stock to hold in the interim, in what form, and where along the value chain.
Some of the components we work with at Merge Technologies are experiencing lead times of up to 12 months, creating difficulties for full functionality installation of our services. The abundance of issues linked to the pandemic, and the global impact this has had on the supply chain has been detrimental in these unprecedented and unexpected lengthy lead times.
Whilst over time, supply chain lines and lead time lengths will improve, it’s all about adapting to what’s in front of you. To combat lengthy lead times, we will continue pulling together temporary loan equipment to get rooms and systems operational (albeit sometimes with reduced functionality) until the new equipment arrives. Thankfully over the years we have accumulated a large pool of loan and demonstration equipment which is enabling us to continue to support this method without any additional costs to our clients.
.jpg)
Utilising alternative hardware, older hardware or even our own office hardware, we can fit rooms out with temporary equipment to ensure that rooms are operational for businesses who need their conference rooms set up promptly, where it is not possible for them to wait for the new equipment.
When the new equipment finally arrives, the loan equipment that was used is replaced with the new equipment, ensuring that rooms are upgraded to full functionality.
Adaptability is key when managing the supply chain problems that we are experiencing across Australia and the world. We’ve taken this onboard at Merge Technologies to ensure we can cope with demand and support thousands of businesses right across Australia.
If you’re interested in learning more about video conference rooms and how they can support your workplace in the future, click here.